![[Translate to English:] Kinematische Darstellung der SW-12R II](/fileadmin/_processed_/5/3/csm_star_sw12rii_kinematik_193640730d.png)
SW-12R II
Diameter | 12 mm / 13 mm (option) |
---|---|
Headstock stroke | 135 mm / 30 mm (fixed headstock lathe) |
Machining possibilities | ![]() |
Kinematics & tools
- 5-station tool holder on the front tool post
- 2-station tool holder on the back tool post
- 4-station drilling unit including sleeves on the front and rear side on the back tool post
- 3 + α power-driven tools for cross machining on the front tool post
- 3 + α power-driven tools for cross machining on the back tool post
- 8 + α power-driven tools including sleeves for backworking
- 10 axes
SW
12R II
NEW MEMBER OF THE
SW SERIES: SW-12R II
The new SW-12R II automatic CNC sliding headstock lathe was developed on the basis of the renowned SW-7. The machine is extremely attractive due to its compact size and offers universal use as either a sliding or fixed headstock lathe. The new SW-12 RII is characterised by high speeds on the main and sub spindle (15,000 rpm) and fully independent machining with 3 tool systems.
![[Translate to English:] SW-12R II](/fileadmin/_processed_/9/d/csm_star_sw12rii_vorteile_418dc3ffc9.png)
Advantages
- FANUC 31i-B5 control system with electronic handwheel
- C axis control as standard on main and sub spindle
- fully independent backworking with 8 stations
- convertible from sliding headstock to fixed headstock lathe
- movable control panel
- 2 tool posts for simultaneous machining on the front side
- three fully independent tool systems
- low space requirement
Specifications
General information | SW-12R II |
---|---|
Number of axes | 10 |
Max. rapid traverse speed | 35 m/min |
Weight | approx. 2,100 kg |
Coolant tank capacity | 139 litres |
Dimensions | approx. 1,995 x 920 x 1,700 mm |
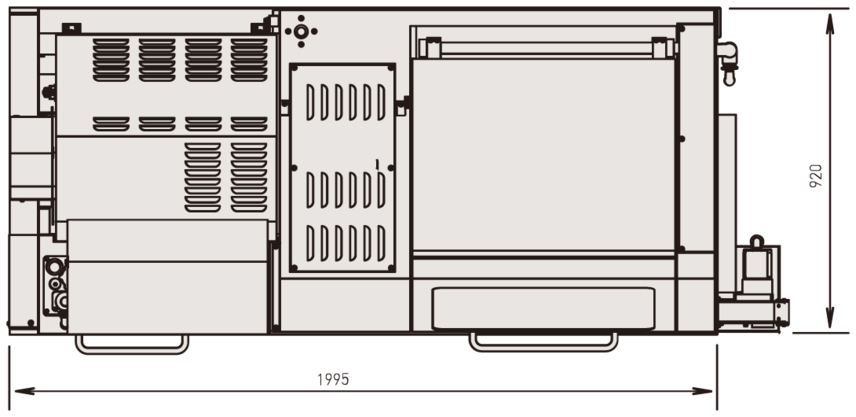
Main spindle side | SW-12R II |
---|---|
Number of axes | 6 |
Axes main spindle (headstock) | Z1 / C1 |
Axes tool post 1 | X1 / Y1 |
Axes tool post 2 | X3 / Y3 |
Max. machining diameter | 12 mm / 13 mm (option) |
Max. headstock stroke (sliding/fixed headstock) | 135 mm / 30 mm |
Max. main spindle drive power | 3.7 kW |
Max. main spindle speed | 15,000 1/m |
Tools on the tool post 1 | |
Turning tools | 5 tools (□ 10 mm) |
Cross machining tools | 3 tools (ER11) |
Max. cross machining drive power | 1.2 kW |
Max. speed cross machining | 12,000 rpm |
Tools on the tool post 2 | |
Turning tools | 2 tools (□ 10 mm) |
Cross machining tools | 3 tools (ER11) |
Max. cross machining drive power | 1.2 kW |
Max. cross machining speed | 12,000 rpm |
Drilling tools (4-spindle drilling unit) | 4 tools (ER11) |
Sub spindle side | SW-12R II |
---|---|
Number of axes | 4 |
Axes sub spindle | X2 / Z2 / C2 |
Vertical axis for backworking | Y2 |
Max. chucking diameter | 12 mm / 13 mm (option) |
Max. sub spindle drive power | 3.7 kW |
Max. sub spindle speed | 15,000 rpm |
Backworking tools | |
Tool stations | 8 units (8 power-driven) |
Max. backworking speed | 12,000 rpm |
Standard scope of delivery
- FANUC 31i-B5 control system with electronic handwheel
- 5-station tool holder on the front tool post
- 2-station tool holder on the back tool post
- 3 + α power-driven tools for cross machining on the front tool post
- 3 + α power-driven tools for cross machining on the back tool post
- 4-spindle drilling unit including sleeves (front and rear side) on the back tool post
- 8 + α power-driven tools including sleeves for backworking
- broken cut-off tool detector
- parts ejection detector
- sub spindle for backworking
- sub spindle air blow unit
- parts receptacle
- pneumatic unit with maintenance unit
- parts ejection detector for the sub spindle
- parts conveyor to remove the parts
- oil lubrication system
- separate coolant tank with level monitoring and coolant flow detector
- bar feeder interface
- levelling pads and adjustment screws
- worklight
- toolbox with special tools
- metric input
- tool nose radius compensation
- constant cutting speed for main and sub spindle
- multiple canned cycles
- operating hours display
- parts counter
- automatic power supply cut-off function
- interfaces to input and read data
- program sequence controllable with electronic handwheel
- cylindrical interpolation
- polar coordinate interpolation
- polygon machining
- 3D coordinate conversion mode
- bar feeding: bar feeder
- chip disposal: chip conveyor
- long parts ejector
- beacon: acc. to customer requirements
- high pressure unit: 50 to 300 bar
- fire protection: small fire extinguishing system
- complete filtration coolant
- Tools in the internet at www.star-tools.eu
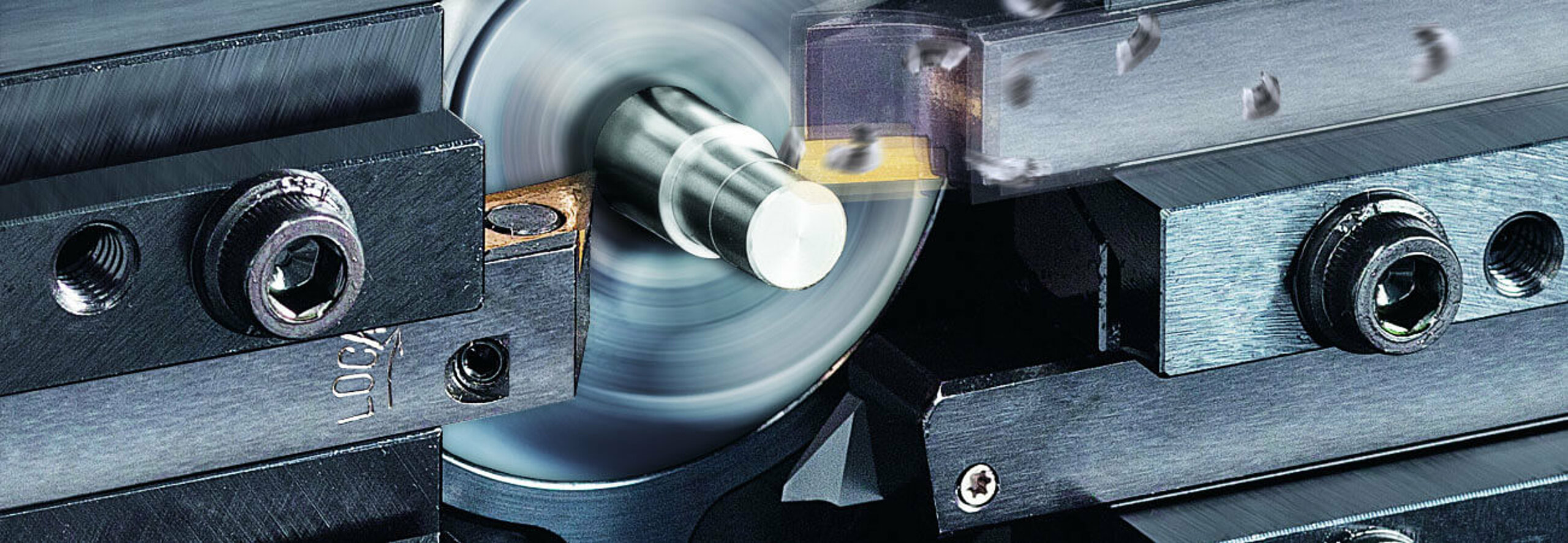
Machining examples
Selection from our
range of tools
Your advantages
with star Micronics
- Training
STAR Micronics GmbH offers special training sessions for machine operators. You as customer can decide whether to have the training in our company or on your premises. The training is naturally exclusively for your personnel and specifically designed for your range of parts. - High pressure unit
The machine can be retrofitted with high pressure units from 50 to 300 bar. In addition, other developments are available to you, such as programmable pressure control or complete filtration. - Cooling lubricants
The machine can be run with oil or with aqueous emulsions. However, we recommend the use of oil as this is far more beneficial to the longevity of the machine. - Bar feeder
All commonly available bar feeders (FMB/IEMCA/LNS) can be used with the machine. The software interface is included in the machine as standard.
- Chip conveyor
The machine can be fitted with a chip conveyor or a chip flushing system. - Peripherals
Peripheral components such as parts separators, purchased coolant units (oil/emulsion), coolant filters, fire protection systems and TPM (tool process monitoring) can also be offered. A retrofit of peripheral components is always possible. - Service
SSC star* Service Connect as 24/7 customer portal and online connectivity for your machines, tickets and service calls. A current overview can be called up at any time. In addition, you have access to the star* knowledge database
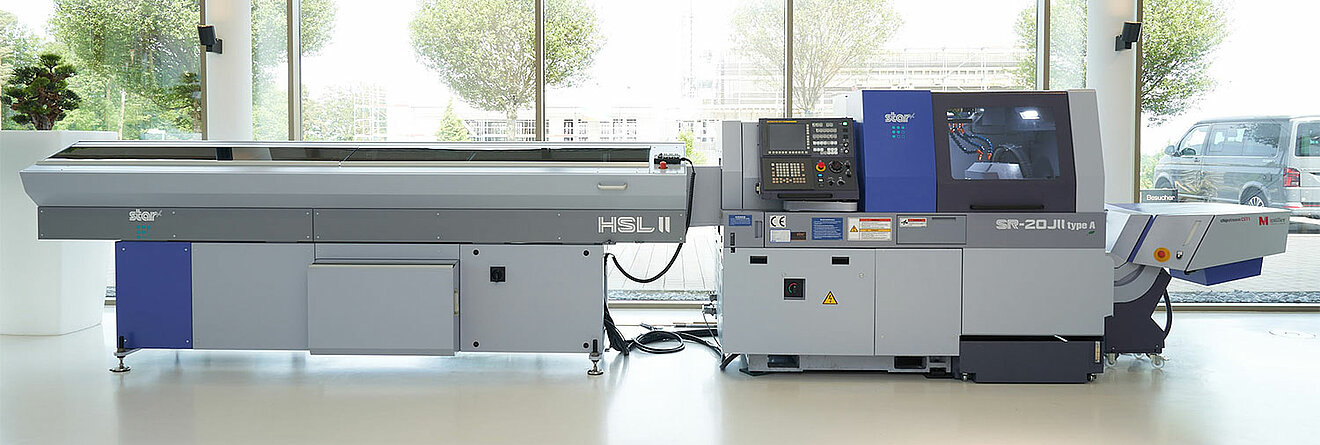
Müller Products can easily be combined with and configured to your star* machine.
REQUEST quotation NOW
You will receive a quotation for a star* SW-12R II with a standard configuration.
Download
SW-12R II brochure
HFT Flyer